Laufzeit:
04/2023 – 03/2025
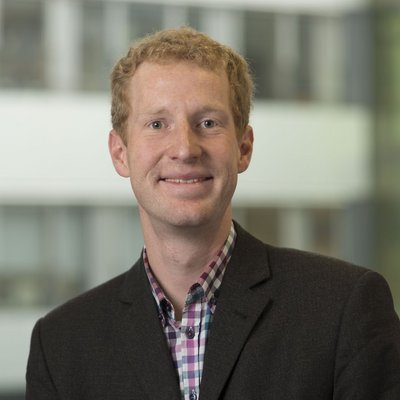
Jan Clausen
Stellv. Abteilungsleiter Gießereitechnologie und Leichtbau
Gruppenleiter Hybridguss
Fraunhofer-Institut für Fertigungstechnik und Angewandte Materialforschung IFAM
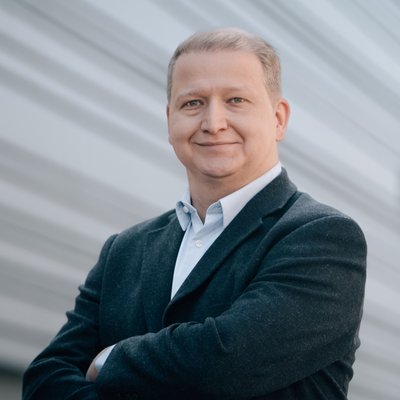
Carsten Lies
Abteilungsleiter Funktionsintegrierter Leichtbau
Fraunhofer-Institut für Werkzeugmaschinen und Umformtechnik
Kreislauforientierte Verbundbauweise aus Kunststoffspritzguss und Aluminiumguss - CirKAL
Vor dem Hintergrund der stets steigenden Anforderungen an Komponenten, deren Entwicklung insbesondere in der Automobilindustrie durch Emissionsreduktion sowie Energieeffizienz sehr stark geprägt ist, wird die Herstellung von Kunststoff-Metall-Hybridbauteilen zu einer zentralen Fragestellung in der Leichtbau-Forschung.
Die unterschiedlichen Materialien lassen sich schon heute durch Form-, Kraft- oder Stoffschuss anwendungs- und funktionsgerecht kombinieren und somit die Vorteile der eingesetzten Werkstoffe nutzen. Neben den zahlreichen Vorteilen hybrider Bauteile – bspw. die Möglichkeit zur Gewichtsreduzierung – bringen die bisher eingesetzten Fertigungstechnologien einige Herausforderungen mit sich. Dazu gehören:
- Lange und komplizierte Prozessketten,
- Erhöhte Ausschussquote durch viele Einzelschritte in der Prozesskette,
- Hoher Investitions- und Platzbedarf für unterschiedliche Maschinen und Anlagen,
- Hoher Prüfaufwand, teilweise mehrfache Prüfung nötig,
- Reduzierte Produktivität (z.B. hoher manueller Aufwand bei Oberflächenbehandlung für Klebverbindungen),
- Ggf. zusätzliche Lagerkapazitäten und/oder Transportwege innerhalb der Fertigung notwendig.
Um die oben genannten Problemstellungen zu umgehen, stellt sich eine vollständige Hybridisierung der Fertigungsprozesse bzw. Fertigungswerkzeuge als eine logische Folge der Hybridisierung der Bauteile dar.
Vorgehen im Projekt
Im Rahmen des Projektes – CirKAL wird eine neue Kombination der Verfahren Spritzguss und Niederdruckkokillenguss unter wirtschaftlichen Randbedingungen erarbeitet, indem Bauteile bedarfs- und materialgerecht in einem kombinierten One-Shot-Werkzeug und damit in kurzen Prozessketten seriennah hergestellt werden. Eine spätere Wiederlösbarkeit der Verbindung und eine Trennbarkeit der beiden Werkstoffkomponenten wird von Anfang an berücksichtigt. So wird ein kreislaufwirtschaftlicher Ansatz für eine Wiedergewinnung der verwendeten Materialien verfolgt.
Die für das Projekt zugrundeliegende Arbeitshypothese geht von der grundsätzlichen Annahme aus, dass erforderliche Maßnahmen zur Sicherstellung der optimalen Kunststoff-Aluminium-Fügeverbindung aus technischer, aber auch wirtschaftlicher Sicht in den kombinierten Fertigungsprozess integrierbar sind. Im Gegensatz zu bereits gelaufenen Arbeiten zeichnet sich die untersuchte Prozesskombination durch neue Herausforderungen aufgrund stark unterschiedlicher Prozesszeiten und Werkzeugtemperaturen aus. Die Adaptierung der jeweiligen Prozesse sowie die besondere Temperaturführung des Werkzeuges durch eine thermische Abkopplung und eine bereichsabhängige Temperierung, um diese für den Betrieb nutzbar zu machen, stellt eine klare Abgrenzung zum aktuellen Stand der Technik dar. Als besonders wichtigen Aspekt wird im Vorhaben das Spannungsfeld zwischen mechanisch stabilem Verbund während des Produktlebenszyklus und einer wieder trennbaren Verbindung am Ende des Produktlebenszyklus adressiert. Dabei steht eine sortenreine Trennung der verwendeten Materialien im Fokus.
Um eine optimale Kunststoff-Aluminium-Fügeverbindung in einem Bauteil zu erzielen, wird zunächst eine Reihe von experimentellen Untersuchungen zur Oberflächenvorbehandlung, -strukturierung sowie -temperierung durchgeführt und als konkrete Empfehlungen für die weiteren Arbeiten zusammengefasst. Dabei wird parallel betrachtet, dass die Fügepartner und die Verbindung gute technische Eigenschaften aufweisen, sich jedoch ebenfalls wieder mit wenig Aufwand sortenrein trennen lassen, um die Einzelkomponenten in weiteren Lebenszyklen weiterverwenden zu können. Das im Rahmen des Vorhabens vorgeschlagene Fügekonzept wird im Kontext einer seriennahen Produktion weiterentwickelt und anhand eines Demonstratorbauteils erprobt, charakterisiert und bewertet. Dafür stehen am Fraunhofer-Standort Wolfsburg in der Open Hybrid LabFactory (OHLF) eine Niederdruckgießanlage und ein Bolt-On-Spritzgussaggregat zur Verfügung. Für diese Anlagen wird ein hybrides Niederdruckguss- und Spritzgusswerkzeug unter der Berücksichtigung der jeweiligen technischen Randbedingungen und unter Einbeziehung der Ergebnisse aus den Vorversuchen ausgelegt und umgesetzt. Dieses kombinierte One-Shot-Werkzeug soll die Herstellung der Kunststoff-Metall-Hybridbauteile mit den Vorteilen beider Verfahren auch hinsichtlich der gießtechnischen Strukturierung der Kontaktfläche sowie der Erzeugung von Hinterschneidungen ermöglichen.
Projektziel
Die Realisierung von komplexen Materialverbunden erfreut sich einer stetigen Nachfrage, dessen Fokus in einer effizienten Realisierbarkeit liegt. Die Ergebnisse aus diesem Forschungsvorhaben sollen genau diesen Bedarf bedienen und die Prozesse Aluminium-Niederdruckkokillenguss mit Kunststoffspritzguss in einem komplexen, aber effizienten Werkzeug abbilden sowie zusätzlich für eine zirkuläre Einsetzbarkeit der verbundenen Werkstoffe sorgen.
Projektkonsortium
Begleitender Ausschuss
- MOLDFIRE - Partner für Entwicklung & Konstruktion
- Schicktanz GmbH
- Tegisa Giessereianlagen und Industrieöfen GmbH
- Nehlsen AG
- ANYBRID GmbH
- LANXESS Deutschland GmbH
- PINTER GUSS GmbH
- Plastics Engineering Group GmbH