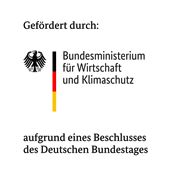
Laufzeit:
Januar 2022 – Dezember 2024
Förderung:
Bundesministerium für Wirtschaft und Klimaschutz (BMWK)
Projektträger:
Projektträger Jülich (PTJ)
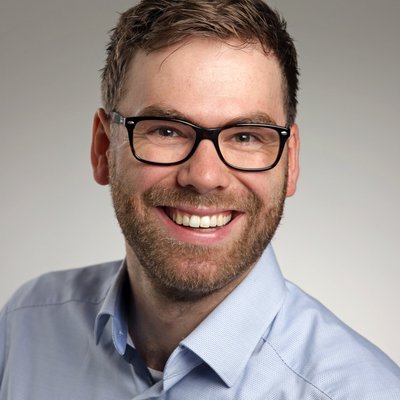
Arne Wagner
Abteilungsleiter Montage und Fertigungsautomatisierung am
Institut für Werkzeugmaschinen und Fertigungstechnik der TU Braunschweig
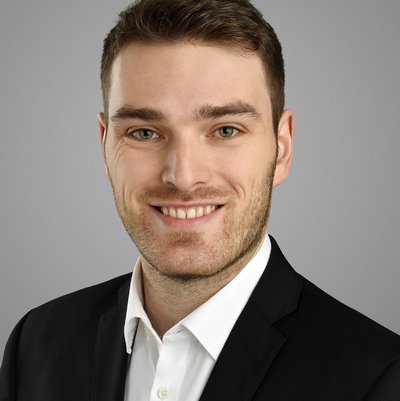
Jan Middelhoff
Wissenschaftlicher Mitarbeiter „Numerische Methoden" am
Institut für Werkzeugmaschinen und Fertigungstechnik der TU Braunschweig
essPresso
Material-, Prozess- und Werkzeugentwicklung zum Hochdurchsatz-Niedertemperatur-Pressen von Graphit Polymer BPP für Heavy Duty Anwendungen
Projektmotivation
Bei der Umstellung von fossilen auf erneuerbare Energieträger gilt grüner Wasserstoff insbesondere aufgrund der großen Bandbreite an Einsatzmöglichkeiten als einer der zentralen Hoffnungsträger bei der Energiewende. Neben der Verwendung bei z. B. der Herstellung von klimaneutralem Stahl, bietet sich der Einsatz von Brennstoffzellen für Heavy-Duty-Anwendungen im Bau (z. B. Generatoren, Pumpen) und im Verkehrswesen (z. B. Bus, LKW, Schiffe, Traktoren) an. Hohe benötigten Stückzahlen der Einzelkomponenten zeigen den Bedarf für Produktionsprozesse mit hoher Produktivität sowie hoher Prozesszuverlässigkeit.
Im Forschungsprojekt essPresso wird für eine Teilkomponente der Brennstoffzelle, die Bipolarplatte (BPP), ein hochproduktiver und innovativer Prozess untersucht. Diese BPP können entweder auf Basis von Graphit oder aus metallischen Materialien hergestellt werden. Aufgrund der besonders korrosiven Atmosphäre innerhalb der Brennstoffzelle bieten BPP auf Basis von Graphit eine deutlich höhere Nutzungsdauer als metallische BPP. Im Rahmen des Forschungsvorhabens werden die BPP aus einem Graphit-Polymer-Compound (GPC) in einem innovativen Pulverpressprozess hergestellt. Neben der geometrischen Gestaltung beeinflusst insbesondere die elektrische sowie die thermische Leitfähigkeit die Zellperformance. Um diese zu maximieren, werden besonders hohe Anteile von Graphit und weiteren Leitadditiven im GPC eingesetzt. Im Gegensatz dazu stehen die Anforderungen an die Zelldichtigkeit, welche durch einen höheren Anteil an Polymer verbessert wird.
Ziel des Projektes ist es, in dem untersuchten Prozess vorerst eine Zykluszeit von 10 s pro BPP zu erreichen. Einer der zentralen Ansätze ist hierbei, die Temperatur während der Formgebung im Pulverpressprozess zu minimieren. Dies soll ermöglichen, die Festigkeit der BPP möglichst hoch zu halten, sodass diese direkt nach dem Pressen schädigungsfrei entformt werden kann. Der dadurch entstehende isotherme Pressprozess ermöglicht eine Reduzierung des Energiebedarfs bei gleichzeitig höherer Produktivität im Vergleich zu einem variothermen Prozess. Besonders herausfordernd ist hierbei das Material so zu modifizieren, dass sowohl die Anforderungen an die elektrische und thermische Leitfähigkeit als auch an die Gasdichtigkeit erfüllt werden. Darüber hinaus müssen die Prozessparameter hinsichtlich der Produktivität optimiert werden und neue Lösungsansätze für nachgelagerte Prozessschritte entwickelt werden um den Gesamtprozess weiter zu verbessern.
Vorgehensweise
Das Projekt wurde im Zuge von Ergebnissen aus ausgedehnten Vorversuchen beantragt und gliedert sich in vier Arbeitspakete. Den ersten Arbeitsschwerpunkt bildet dabei eine Anforderungsanalyse für das Material, den Prozess und das Werkzeugsystem. Hier kann ebenfalls auf Ergebnisse aus den Vorversuchen zurückgegriffen werden, sodass bereits mit Projektstart ein umfangreiches Prozesswissen vorlag. Auf Basis der ermittelten Anforderungen wird eine Versuchsplanung sowohl für die Materialentwicklung als auch für die Prozessentwicklung erarbeitet. Im zweiten Arbeitspaket wird die Materialentwicklung fokussiert. Hier werden zunächst geeignete Compounds aus Graphit und Polymer sowie verschiedener Additive analysiert und hinsichtlich ihrer industriellen Großserienfertigbarkeit untersucht. Neben den thermoplastischen Rezepturen werden auch duroplastische Materialkombinationen betrachtet. In enger Abstimmung mit der Materialentwicklung und auf Basis der Ergebnisse aus den Vorversuchen wird der Gesamtprozess zur Herstellung der BPP entwickelt. In diesem Kontext werden das Werkzeugsystem, das Füllsystem sowie Greif- und Handhabungssysteme entwickelt. Diese Einzelsysteme werden im Arbeitspaket 3 betrachtet und führen in einem zweiphasigen Ablauf von einem Demosystem zu einem optimierten Gesamtsystem. Im Arbeitspaket 4 wird aufbauend auf den Erkenntnissen aus der Materialentwicklung und in enger Zusammenarbeit mit der Entwicklung des Befüll-, Greif- und Handhabungs- sowie Werkzeugsystems der Gesamtprozess mit den notwendigen nachgelagerten Prozessschritten entwickelt und hinsichtlich der Parameter optimiert.
Durch den schrittweisen Aufbau und die enge Abstimmung der Projektarbeitspakete mit übergreifenden Schnittpunkten wird eine ganzheitliche Betrachtung von Material- und Prozessentwicklung auf prototypischer Ebene gewährleistet.
Ansätze und Nutzen (Projektziele)
Im Fokus des Projektes esspresso stehen Graphit-Polymer-BPP bzw. BP-HP mit dünnen Wandstärken (< 0,3 mm), feinen Kanalstrukturen (0,3 mm Breite und Höhe) variabler Geometrie (V-Querschnitt, runder oder rechteckiger Querschnitt) und einem hohen Graphitfüllgrad (~90%). Die angestrebte Zykluszeit des Pressprozesses beträgt 2,5 – 5 Sekunden. Das übergeordnete Ziel des Vorhabens esspresso besteht darin, die industrielle Großserienfertigung dieser Bipolarplatten mit den geforderten Qualitätseigenschaften und zu den angestrebten Zykluszeiten nach Projektende umsetzbar zu machen. Mittel- bis langfristig verfolgt das geplante Vorhaben außerdem das Ziel, für den Produktionsstandort Deutschland die Technologieführerschaft im Bereich der Werkzeugmaschinen zum automatisierten Pressen mit Befüllung, Formgebung und Handhaben von GP-BPP aufzubauen. Der Kern-Lösungsansatz zur Erreichung des Projektziels besteht in der ganzheitlichen Erforschung von Graphit-Polymer-Material und Niedertemperatur-Pressprozess in Verbindung mit erforderlichen Werkzeugtechnologien. Aus dem Projektziel ergeben sich die folgenden Teilziele:
Teilziel 1: Erfolgreiche Erforschung geeigneter Rezepturen eines Graphit-Polymer Materials für ein Niedertemperatur-Pressverfahren im Bereich von 90 bis 160 °C zur Herstellung von BP-HP. Die Erreichung dieses Ziels ermöglicht die Reduktion von Heiz- und Kühlphasen und verkürzt damit signifikant die Zykluszeit des Pressprozesses. Gleichzeitig wird damit auch erheblich der energetische Aufwand für die Temperierung im Pressprozess je Zyklus, um 40 bis 77,8% reduziert, was bei ca. 2,4 Millionen Presszyklen im Jahr je Presse eine Einsparung im Bereich von 76 bis 165 MW bedeuten kann.
Teilziel 2: Erfolgreiche Erforschung eines Niedertemperatur-Pressverfahrens. Im besten Falle (z. B. bei etwa 90 °C) findet ein isothermer Presszyklus ohne separate Heiz- und Kühlphase statt. Ist dies nicht umsetzbar, liegt der Fokus auf einer dem Pressprozess nachgelagerten, entkoppelten Temperstrecke zur Sicherstellung der Gasdichtigkeit der Presslinge.
Teilziel 3: Simultanes Pressen von mehreren GP-BP-HP in 10 Sekunden. Dies entspricht einer Zykluszeit pro Halbplatte von bis zu 2,5 Sekunden bei der gleichzeitigen Fertigung von vier Halbplatten.